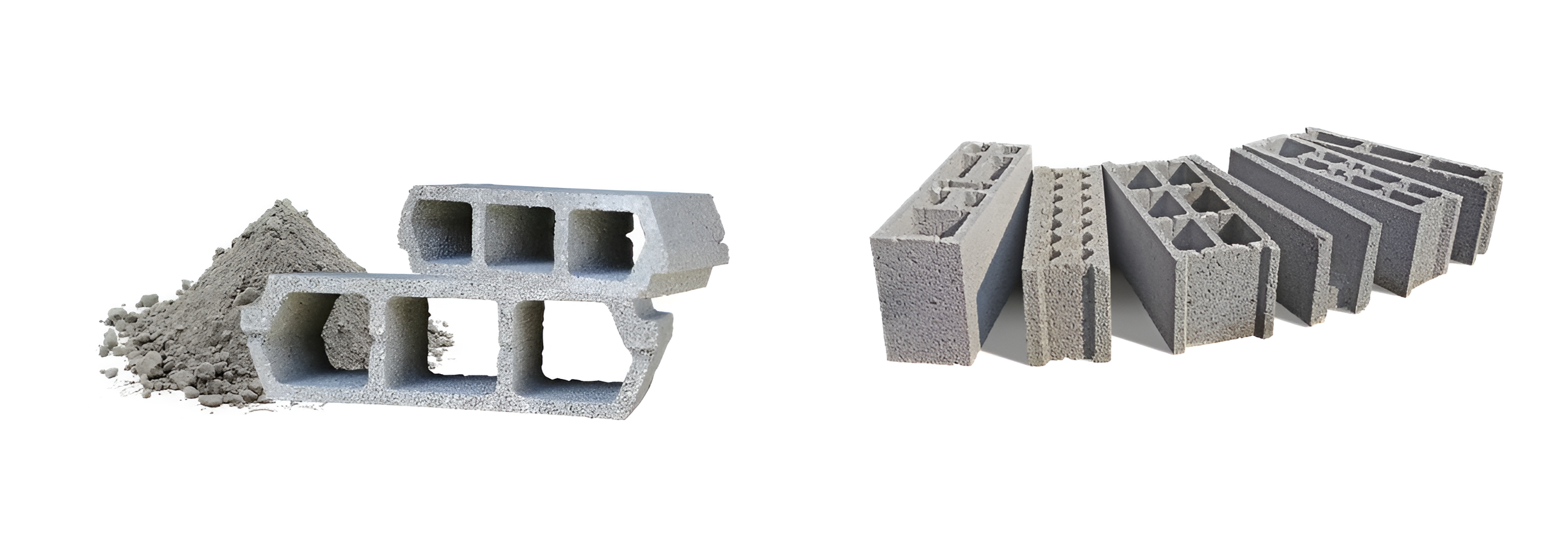
What are Briquette Lines and Machines?
Briquette lines are sophisticated systems engineered to transform various raw materials, such as sawdust, biomass, coal, and other industrial by-products, into highly compressed blocks or briquettes. These briquettes are extensively used across industries like construction, agriculture, and manufacturing due to their compact form, high density, and versatility. Briquette machines are designed for efficiency, durability, and consistent production, catering to the needs of both small-scale businesses and large industrial operations.
Beyond their practical applications, briquette machines play a crucial role in waste management by converting by-products into valuable resources. These machines contribute to sustainability by reducing waste, cutting costs, and providing an eco-friendly alternative to non-renewable energy sources. Similarly, block machines specialize in crafting high-quality bricks and structural components essential for construction projects, enabling businesses to meet growing demands with precision and efficiency.
Together, briquette and block machines offer innovative solutions that enhance productivity, promote environmental responsibility, and support the development of greener, more sustainable industries. Their versatility and advanced technology make them indispensable tools for transforming raw materials into valuable, usable products while reducing environmental impact.
MGB600 Briquette Machine
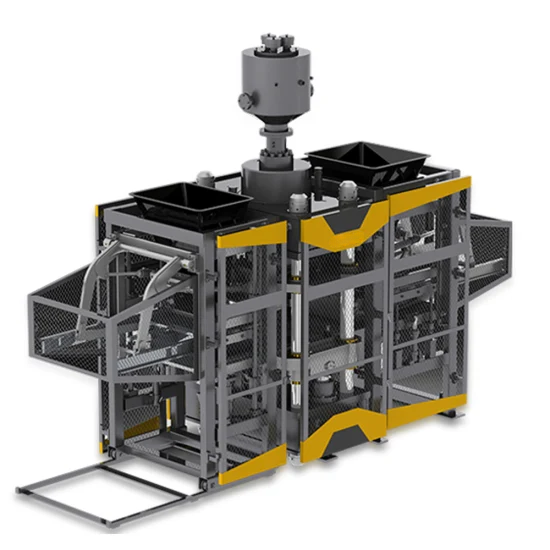
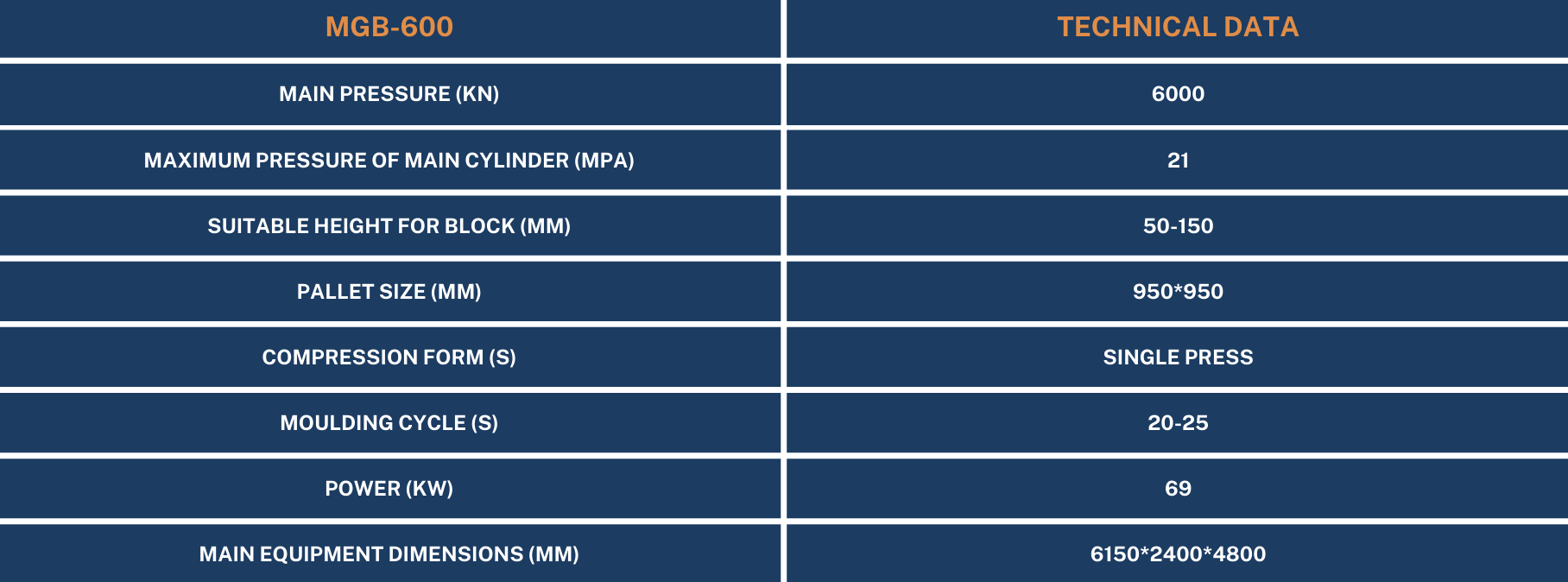

The equipment adopts a micro-vibration feeding system, which enhances feeding efficiency significantly. It is capable of producing high-strength paving stones, slope protection bricks, terrazzo tiles, clay bricks, and more. With Siemens PLC control, the machine integrates and automates electrical, hydraulic, and mechanical systems. It also features a user-friendly man-machine interface, complete with automatic fault diagnosis, remote monitoring, and fully automated operation procedures. The system boasts advanced automation, utilizing Siemens PLC control to enable seamless operation, including remote monitoring and troubleshooting capabilities. The dual-motor material distribution system allows for precise control of front and rear material distribution times on the same pallet, ensuring balanced and efficient feeding. Equipped with a vibrating table micro-vibration system, the machine ensures faster and more uniform feeding while maintaining low noise levels for improved operational efficiency. Additionally, the equipment is versatile enough to produce dry PC terrazzo tiles, further broadening its range of applications.
MGC1000 Briquette Machine
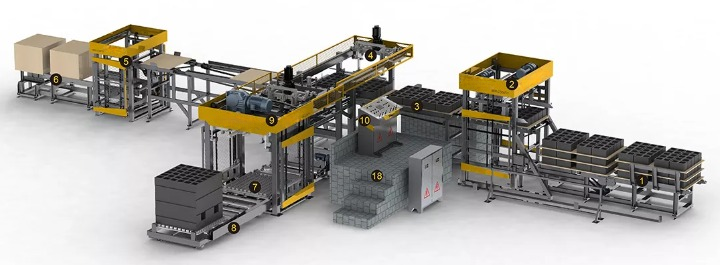
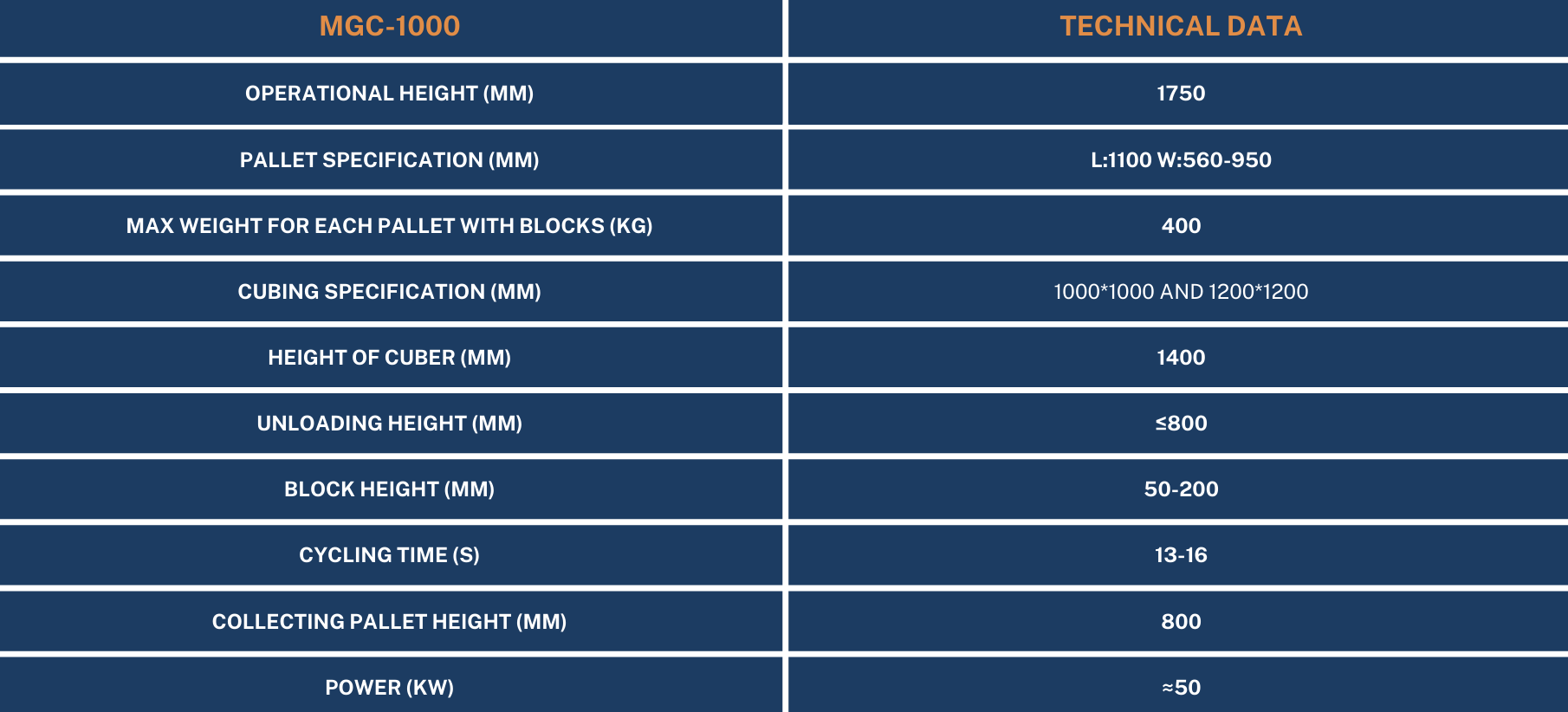
Main Technical Features
The cuber system is highly versatile, accommodating pallets of various specifications. Different block types can be separated with pallets, rearranged, and stacked in a cross-type configuration to form the desired cube. Forklift transport holes can be reserved automatically.
After stacking, the complete cube is conveyed out and can either be manually packed or wrapped using an automatic wrapping machine.
Blocks can be stacked with or without trays, providing flexibility for different applications.
Fully automatic operation is achieved through real-time, high-speed data exchange over Ethernet and high-end intelligent sensors. The control system features automatic fault alarms, machine stop upon faults, and detailed prompts for troubleshooting, simplifying maintenance without requiring professional personnel.
Components
- Block Unloading Conveyor
- Block Unloading Machine (two pallets)
- Composite Conveyor
- Block Pushing Machine
- Pallet Receiving Machine
- Pallet Receiving Conveyor
- Cuber Tray (with transferring holes reserved)
- Cuber Conveyor
- Low Position Cuber
- Control System
Optional Components
- Pallet Brushing Machine
- Pallet Turnover Machine
- Oiling Machine
- Tray Bin
- Pallet Conveyor
- Pallet Return Conveyor
- Plate Conveyor
- Operating Platform
MGS2000 Briquette Machine
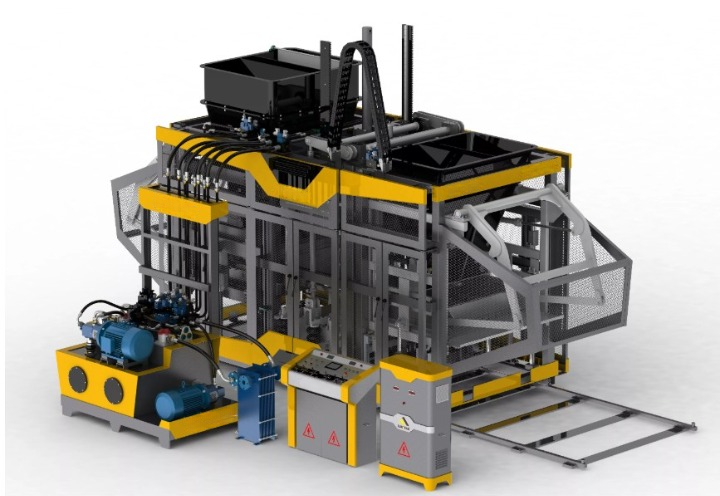
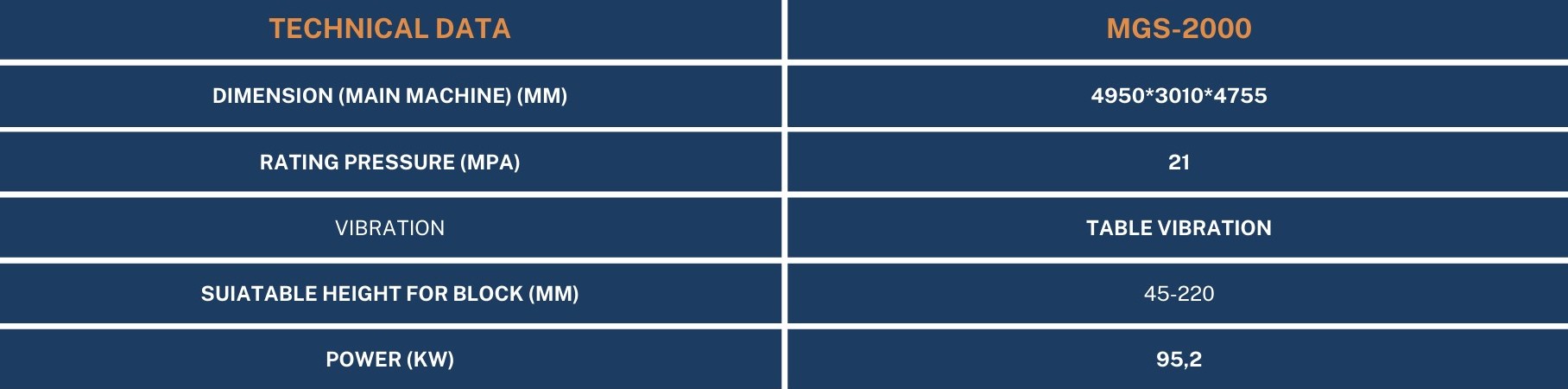
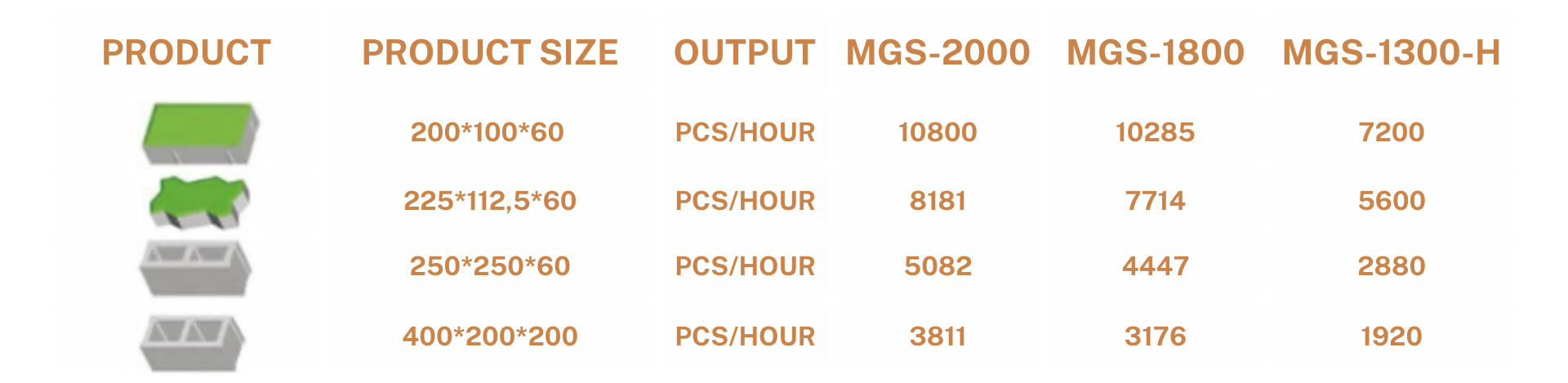
Main Features of the Product:
- High-efficiency servo system: Utilizes a high-efficiency two-axis servo to enable high-speed, high-frequency vibration with excellent synchronization, energy saving, and noise reduction.
- High-efficiency hydraulic control system: Powered by a high-horsepower double-pump motor, offering high efficiency, flexible movements, and quick response times.
- Airbag clamping: Reduces sound and noise, speeds up mold changes, and minimizes mold damage.
- Damping pad: Made from imported Michelin raw rubber, providing efficient damping, noise reduction, and long-lasting durability.
- Double pressure head cylinder design: Improves product strength and quality.
- Rotary feeder: Features a 360 degree rotating rake with a scraping device, ideal for producing high-quality tiles with wide applicability.
- Anti-mixing pigment feeding system: Prevents pigment mixing and enhances the surface quality of tiles.
- Auxiliary automatic mold changing system: Enables quick mold changes, boosting production efficiency.
- Intelligent control: Equipped with Siemens PLC for core control and renowned sensors like German Turck. Offers simple operation, full fault alarm, and automatic diagnosis functions, significantly reducing troubleshooting time.
8 Advantages:
- Expert in concrete block making machine industry: Ensures expertise and reliability in production.
- Intellectualized control: Achieves a 15% saving in labor costs.
- Electro-hydraulic integrated technology: Raises output by 20%.
- Suspension type vibration: Reduces noise pollution by 10%.
- Fault alarm system: Saves 30% of time during troubleshooting.
- Intellectualized starting: Improves working efficiency by 20%.
- Material-ratio program: Saved in the PLC controller to eliminate human error.
- Intelligent remote control: Offers quick problem resolution anytime and anywhere.
- Customized design: Enhances production efficiency while reducing costs.